Ben Fitzgerald on the game-changing AMR Technology Campus and what it takes to get an F1 car on the track
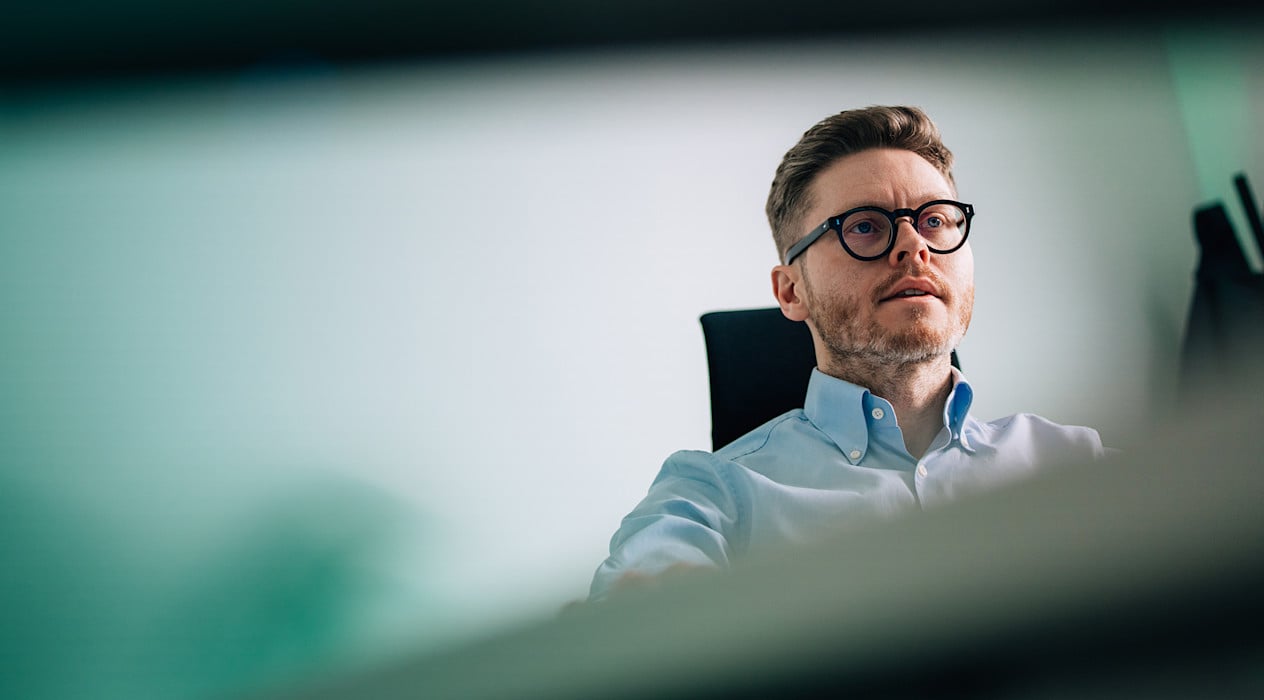
Car build, cost caps, technical directives, a state-of-the-art campus... and 2026. Chief Operating Officer Ben Fitzgerald talks all this and more as he opens up about the relentless pursuit of efficiency and performance at Aston Martin Aramco.
From the AMR Technology Campus to the racetrack, Chief Operating Officer Ben Fitzgerald oversees the production and delivery of every single part of our Formula One cars.
After a packed period where we've launched our new car, tested it in Bahrain, and completed a season-opening double-header in Australia and China, Ben reveals how the AMR Technology Campus is making our car-build process more efficient than ever and how we'll tackle the challenge of balancing a 24-race calendar this year with preparing for the sport's major regulation changes in 2026.
Ben, it's been a very busy few months for the team, building the AMR25 and getting it on track for testing and the first races of the season. How did we evolve and improve our processes ahead of the 2025 campaign?
"Car build is always a busy time for any F1 team because it is the coming together of a lot of vehicle developments and functional collaborations through the winter.
"CEO & Team Principal Andy Cowell set us the challenge of finding a way to take time out of the engineering and manufacturing processes to create more time for the aerodynamic department to work on their designs, which started being released in October last year.
"We generated about 85 weeks' worth of additional time by stretching the engineering and manufacturing capacity – a real step change compared to what we'd done in prior years.
"For the first time, we also delivered two full cars to pre-season testing. We had zero mechanical faults in Bahrain – testament to good quality preparation and production – and we delivered a third chassis in time for the Australian Grand Prix.
"We produced 75 per cent of our parts in-house, a seven per cent increase on last year, and in February our output was 3,666 parts being produced every week."
At the start of a new season, what is the key focus for you and your team?
"This time of year, the priority is to push hard to build our quantity of parts that the race team needs for testing and the early races. For the Australian and Chinese Grands Prix, the biggest challenge was ensuring we had adequate quantities of all vehicle options.
"We like to have at least four of the majority of the part assemblies, if not more, built by race one, rising further for race two. For example, for Australia this year, we had four front wings, for China we had five, and for Japan we'll have six.
"Of course, we have updates in the pipeline this year as well, so our challenge is to get parts trackside and allow the team to race with adequate quantities in the early races before our focus in the supply chain and manufacturing turns to new designs for our update packages."
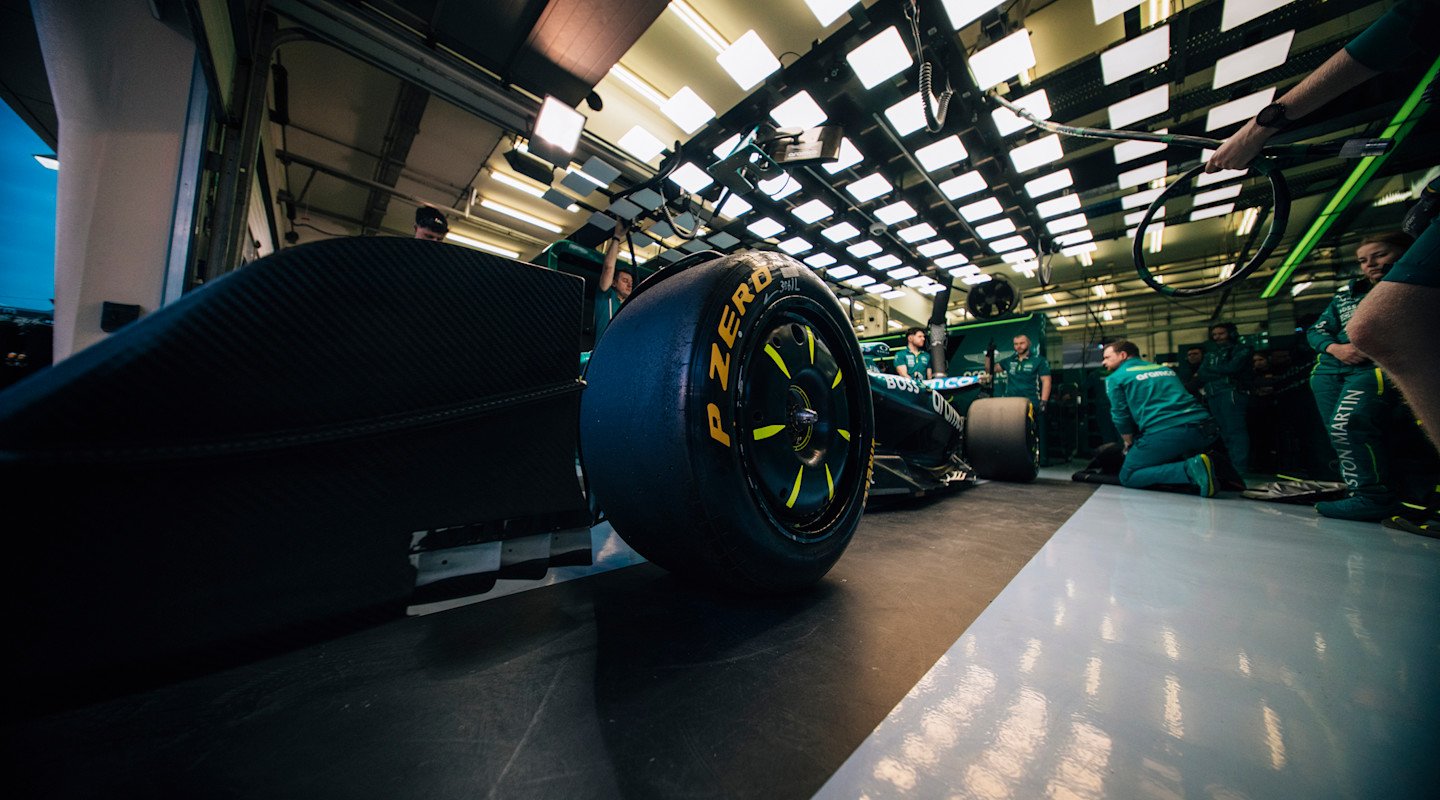
What are the biggest challenges you're likely to face over the course of this 24-race season?
"We get to our minimum quantity of parts level as quickly as possible and then we start rationalising quantity versus cost.
"For example, if we build six sets of suspension for race one and then the strategy of suspension setup and shrouds changes, we have to mitigate the impact to the cost cap budget, providing funds for future development.
"It's the same when a technical directive is issued by the FIA. For example, there's one coming at the Spanish Grand Prix concerning front wing elasticity. We'll have to produce a design which adheres to that and therefore the previous spec becomes redundant, meaning we need to build up stock of the new wing.
"That's what we're trying to stay on top of a lot of the time.
"However, this year, what we also need to do alongside working through quantities versus cost cap versus updates, is consider what capacity we have available in the AMR Technology Campus to focus on AMR26..."
The aerodynamics department is working on both 2025 and 2026. In engineering, the main focus right now is on early-season updates for AMR25.
2026 sees a swathe of technical regulation changes. How much are we already focusing on these changes, and how are we striking a balance between development of the AMR25 and next year's car?
"This year, we're doing much more development for future programmes in-year than we have in the past.
"The aerodynamics department is working on both 2025 and 2026. In engineering, the main focus right now is on early-season updates for AMR25.
"As the 2026 aero releases are sent to the engineering team, and the proof of concepts starts to turn to design into production releases, that's when we'll see a real shift towards 2026 development. I think we're probably eight to 10 weeks away from that.
"From a manufacturing perspective, we're already producing proof of concept chassis for 2026. The carbon main case for the rear end for 2026 is currently having its tooling machined and we'll be laminating that within the next five weeks or so.
"The gearbox casings are well progressed and the gearbox dyno is running in the AMR Technology Campus."
For the first time in about 20 years, everybody in the team is in one location at the AMR Technology Campus.
Our new wind tunnel is online. How big a milestone is this on the team's journey?
"Having the new wind tunnel online is a massive milestone for the team.
"When we were using the Mercedes wind tunnel, we had to manage our test programmes between Friday and Sunday, using the weekdays in between to refine and reproduce test items.
"Now, we'll get the same number of runs, based on our championship position, but we can go in and out of the tunnel as per our strategy defined by Eric Blandin and the aero team.
"For the first time in about 20 years, everybody in the team is in one location at the AMR Technology Campus: the aerodynamicists, the model assembly technicians, the additive manufacturing department – which produces a lot of the raw material for the models – and the wind tunnel team. The cross-functional collaboration between these teams, though already very strong, will improve and develop even further by being under one roof.
"It will take time for us to optimise the wind tunnel but we're already making use of it and getting great data. It's a huge step forwards for the team."
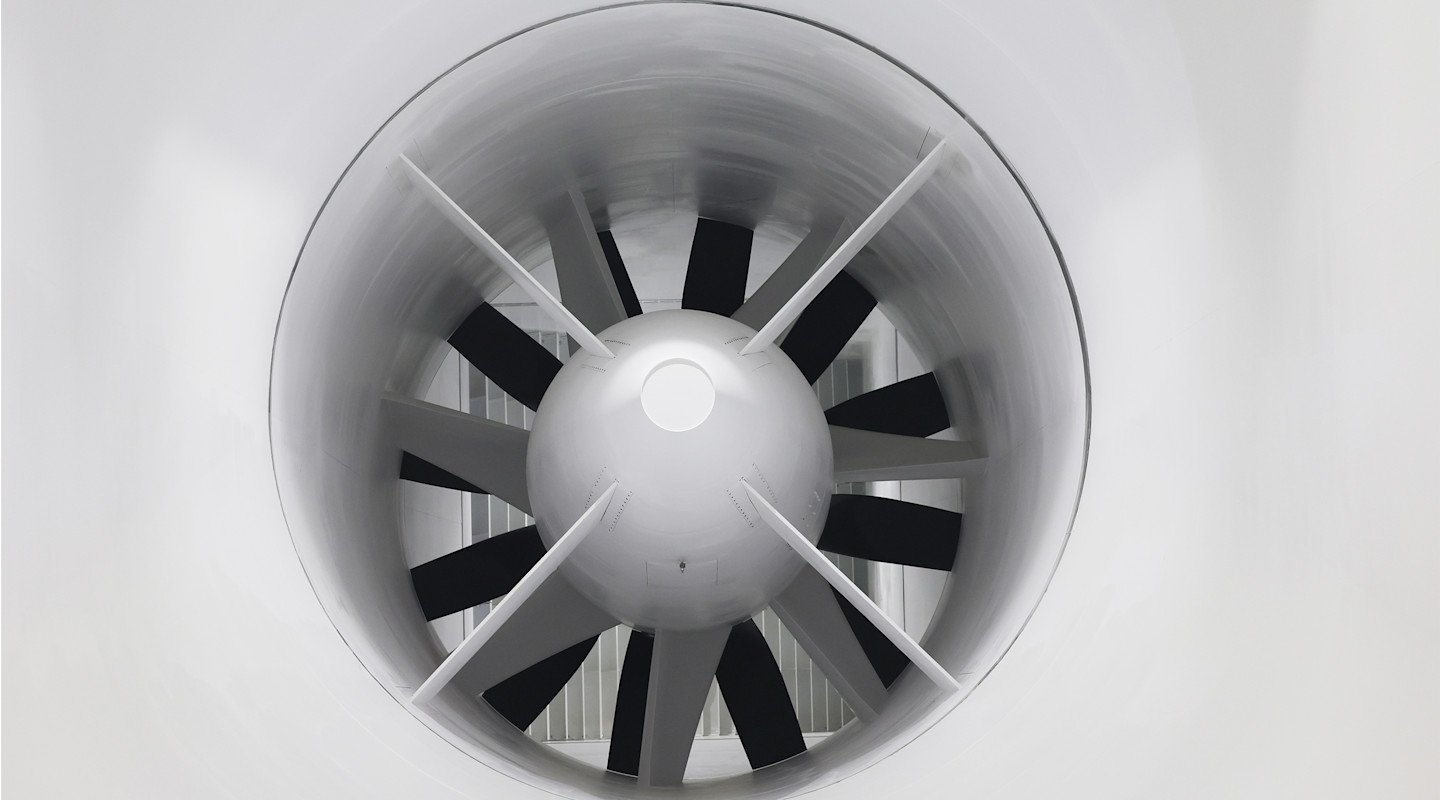
The AMR Technology Campus is home to an array of state-of-the-art tools. How do we make the most of them?
"We have some of the best tools in the world, but we've got to create an end-to-end programme management function that gives clarity from car concept through to delivery, and develop effective KPIs, frameworks and processes.
"We need to make clear what's required, define and manage the plan well, and drive accountability. The outcome should be a relatively quick F1 car!
"It's about being efficient. One of the key efficiency drivers in the AMR Technology Campus is the flow of components from east to west in the building. We've got composites at one end and race bays at the other where the car is assembled.
"A prime example of the impact our Technology Campus and processes have had on efficiency is in our part production capacity. We've boosted our volume by three-and-a-half times, whilst simultaneously enhancing quality and cutting costs by 33 per cent. Moving forward, we will continue to expand our insourcing, which will further elevate our operational value."
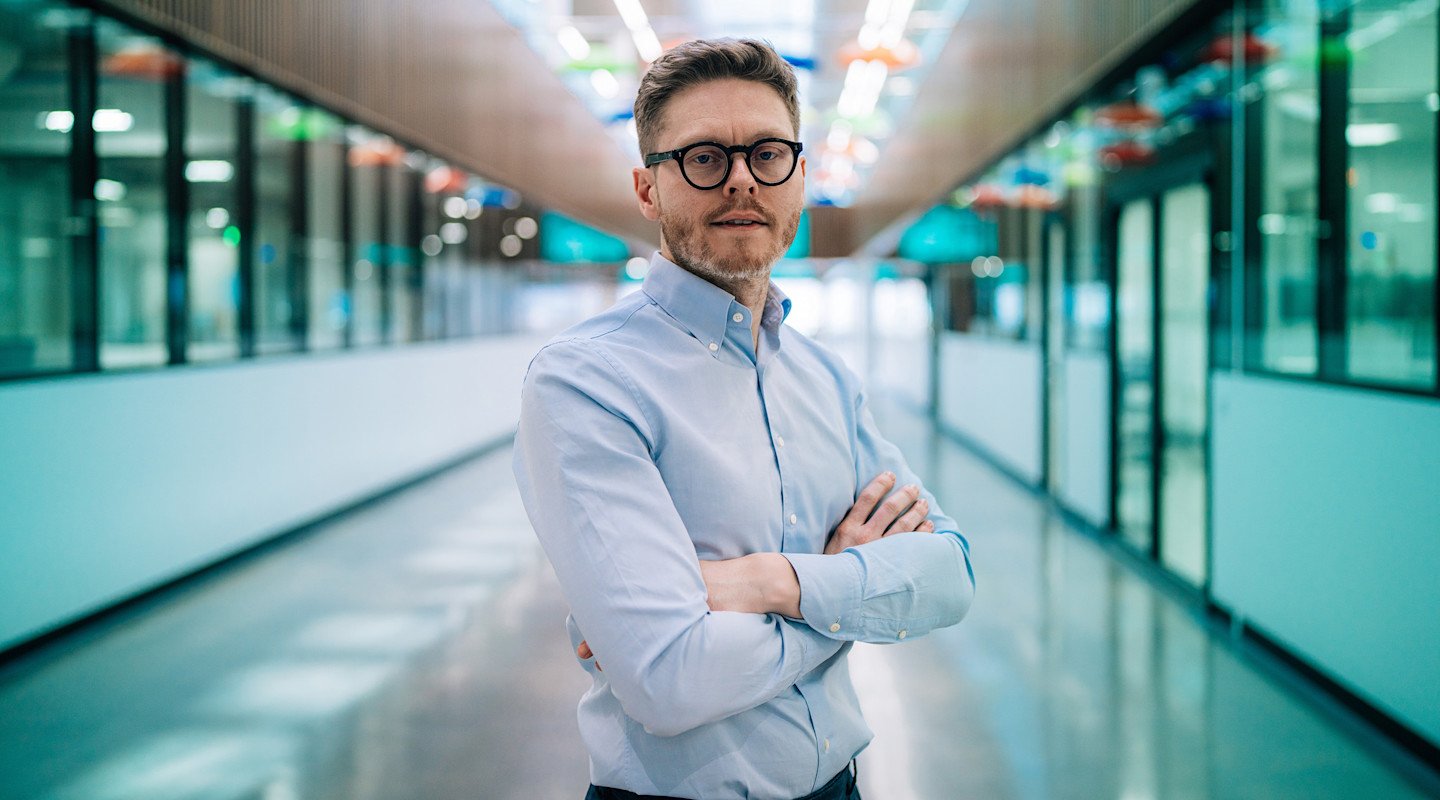
What's your biggest focus each race weekend?
"Ahead of a Grand Prix the focus is twofold: delivering the parts the team needs, which could include updates or track-specific parts, and providing anything extra that's required following the previous race.
"I'm always looking at what the operations team needs to deliver, making sure the team has IT resilience, part quantities and quality issues contained.
"It's also about making sure we react to what happens at the previous race weekend, particularly in a double- or triple-header.
"It's part of the sport that we're going to pick up damage and wear over the course of the year, as was the case following Fernando's unfortunate crash at the Australian Grand Prix, so we've got to produce replacements whilst keeping an eye on the budget cap and continue to deliver future developments.
"It's a constant balancing act but it's one we execute well, meaning our cars are always ready to hit the track from the start of a race weekend."
I / AM membership
The ultimate fan experience.
Get closer to the team with unparalleled access, behind-the-scenes insights and once-in-a-lifetime experiences, and enjoy exclusive competitions, rewards, offers and more.